How Electrocycling GmbH Identifies and Sorts Batteries and Electronic Waste Using AI
The WeSort.AI technology takes waste sorting to a whole new level: it analyzes incoming electronic waste, improves the purity of materials for subsequent recycling processes, and minimizes the risk of fires caused by undetected lithium batteries.
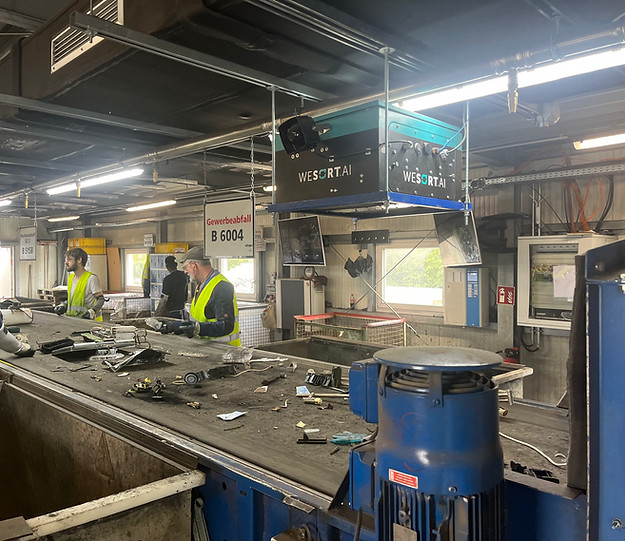
A Leader in Recycling: Electrocycling GmbH
With an impressive processing capacity of up to 80,000 tons per year, Electrocycling GmbH is one of the largest electronic waste recycling companies in Europe. For over 30 years, this company, based in Goslar, has been recycling electronic waste and producing high-quality secondary raw materials, all while prioritizing innovation and sustainability.
​
Before recovery and recycling processes can begin, the end-of-life devices delivered from private households and municipal collections must be carefully sorted. This process is carried out on a sorting conveyor, where up to eight employees per shift remove hazardous components and devices such as batteries, fluorescent tubes, smoke detectors, capacitors, and mercury-containing items. Additionally, disruptive materials and contaminants, including industrial waste, wood, textiles, glass, or ceramics, are removed to ensure optimal processing for subsequent recycling stages.
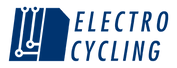
The Challenge: Staffing Shortages and Fire Risks
Like many other companies in the recycling industry, Electrocycling GmbH faces increasing challenges:
​
-
Shortage of qualified personnel: It is becoming increasingly difficult to recruit enough skilled workers for manual presorting.
-
Inconsistent sorting quality: Manual sorting leaves a high risk of undetected batteries or other hazardous materials.
-
Increased fire risk: Overlooked batteries or other dangerous materials frequently cause fires, resulting in significant damage and safety hazards.

"The delivered waste often contains batteries or environmentally hazardous materials. If these are overlooked during manual presorting, contamination or fires in subsequent processes can occur."

Kai Kramer
Quality Management
Electrocycling GmbH
The Solution: Efficient Presorting with AI-Powered Technology
To address the challenges outlined, Electrocycling GmbH has implemented the Vision.Insights system by WeSort.AI in its presorting process. This advanced system is installed directly above the conveyor belt used for manual presorting and leverages cutting-edge camera technology and AI algorithms to precisely identify lithium batteries, battery-powered devices, and other foreign materials.
How the System Works
-
Real-Time Detection: When a battery or hazardous object is identified, the system displays the information on a screen for the sorting staff, accompanied by an acoustic alert to ensure attention is drawn to the item.
-
Process Monitoring: The system continuously tracks how many batteries or other dangerous materials were not sorted out. These statistics are presented in a user-friendly dashboard.
-
Sorting Quality Analysis: The dashboard provides the operations team with detailed insights into the sorting performance of each shift, enabling targeted quality assurance measures.
Versatile Material Recognition
In addition to identifying batteries and battery-powered devices such as tools, small household appliances, smoke detectors, hygiene products, and transponders, the system can detect a wide range of materials, including metals, plastics, textiles, wood, and glass. This versatility makes Vision.Insights an indispensable tool for efficient and sustainable waste management.
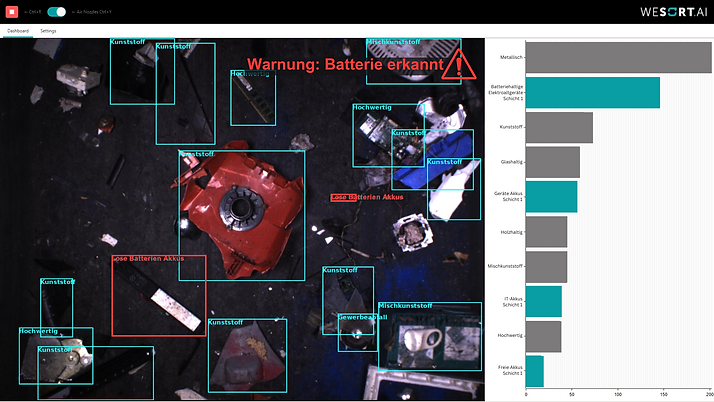
Value Proposition: Prevention Instead of Firefighting
The Vision.Insights system by WeSort.AI provides a truly preventive solution for fire avoidance, offering a proactive approach compared to costly fire suppression measures.
​
Implementing the system has resulted in measurable benefits. Minor fire-related damages, which typically cost around €200,000 annually per facility, can be significantly reduced. Furthermore, the technology safeguards against the potential total loss of entire sorting facilities, which could result in damages amounting to up to €30 million.
​
Additional Benefits of the System Include:
​
-
Preventive Fire Protection: Early detection of hazardous objects like lithium-ion batteries minimizes fire risks.
-
Reduced Insurance Premiums: Lower fire risk translates into more favorable insurance terms.
-
Decreased Property Damage: Fewer damages lead to reduced repair and rebuilding costs.
-
Minimized Downtime: Facilities remain operational and productive even in potential risk scenarios.
-
Lower Financial Reserves: Reduced need for financial provisions for potential incidents.
-
Fulfillment of Contractual Obligations: Uninterrupted processes ensure reliable compliance with contractual commitments.
-
Enhanced Quality Control and Transparency: Detailed data analytics provide insights into material flows, improving process management and operational efficiency.

"The AI system from WeSort.AI can reliably detect even concealed or embedded hazardous components like batteries. It helps us better understand the materials processed through our facility and significantly enhances our operational safety."

Kai Kramer
Quality Management
Electrocycling GmbH
Next Steps: Automating the Pre-Sorting Process
Electrocycling and WeSort.AI are collaborating to further automate the sorting of electronic waste. This includes the implementation of specialized air-pressure nozzles capable of precisely and efficiently removing a wide range of objects, from small battery cells to robotic lawnmowers and even e-bike batteries.
​
This advanced technology marks a significant step toward a fully automated, safe, and efficient recycling facility—enhancing both safety and operational efficiency.

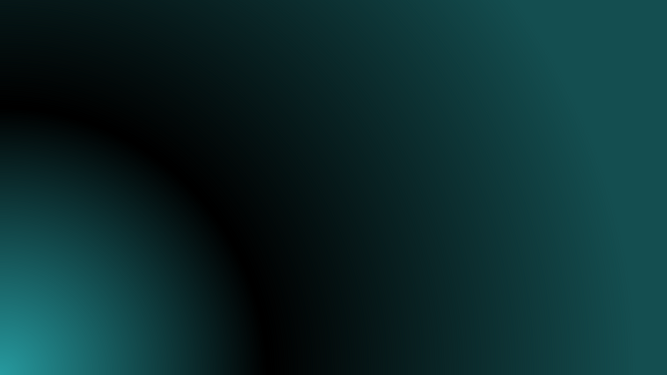
"Our goal in this ongoing collaboration is to fully automate the manual pre-sorting process."

Nathanael Laier
CEO
WeSort.AI GmbH
76 % increased safety
50% purer sorting
Annual EBIT increase of over 600 thousand euros
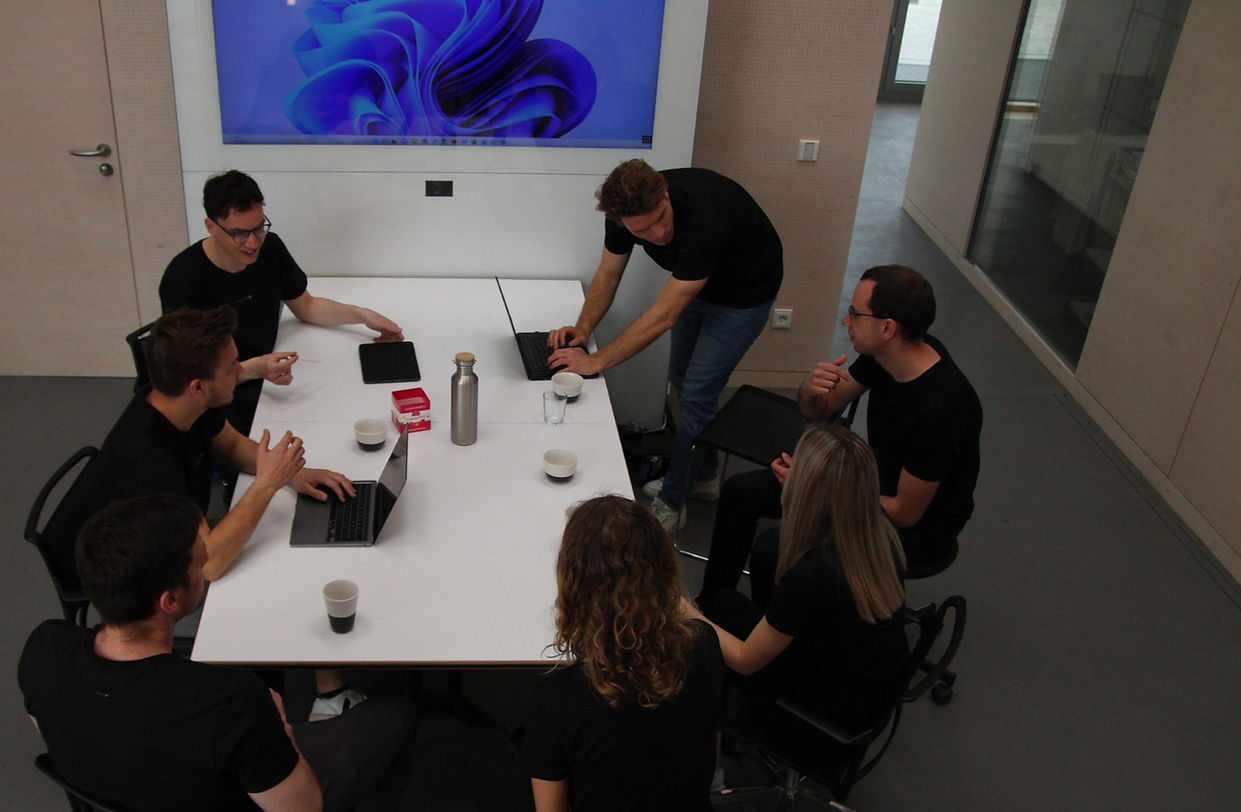